Ultimaker x Make Architects
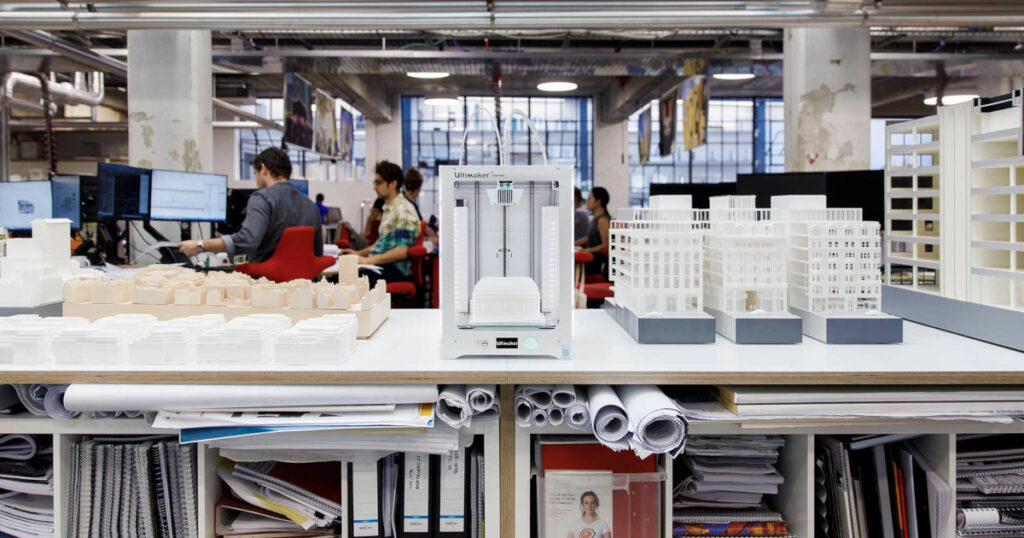
Transformer la fabrication de modèles architecturaux avec une impression 3D abordable Make Architects est un cabinet primé, détenu par ses employés, dont le siège social se situe à Londres. Ses imprimantes 3D Ultimaker soutiennent la culture de conception démocratique du studio, permettant aux concepteurs de modèles et aux autres employés d’imprimer des milliers de modèles chaque année. L’impression 3D facile d’utilisation est intégrée au flux de travail de chaque projet, de la conception à la présentation. Ce cas client est disponible au format pdf. Remplissez le formulaire ci-joint pour recevoir le cas complet.
Raise3D x Hegen
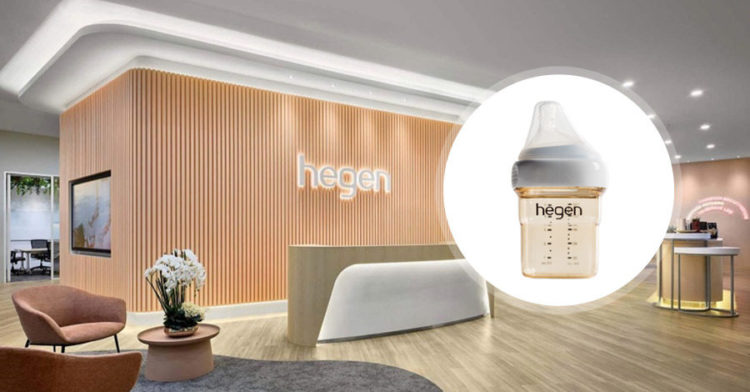
Raise3D Tech donne au géant des biberons Hegen une avance dans son industrie Fondée en 2015, Hegen, marque nationale de biberons à Singapour, a fait sensation dès son lancement. Avec le programme de soins infirmiers multifonctionnel de « pompage, stockage, alimentation » et un certain nombre de prix de design, elle est devenue une marque de renommée mondiale pour les mères et les bébés. Hegen vient de l’allemand « hegen und pflegen », qui signifie « chérir et soigner ». Avec près de 100 biberons de haute qualité, Hegen protège l’expérience d’alimentation sûre et agréable de millions de mères à travers le monde. L’innovation a toujours été la compétence principale de Hegen. Avec l’aide et l’imprimante Raise3D d’ELH Additive manufacturing, fournisseur de solutions de fabrication additive et distributeur de Raise3D à Singapour, Hegen est en mesure d’innover en matière de produits. La Raise3D E2 accorde à Hegen des capacités de production flexibles, avec divers matériaux et une facilité d’utilisation pour les ingénieurs. Ce cas client est disponible en anglais au format pdf. Remplissez le formulaire ci-joint pour recevoir le cas complet.
Ultimaker x Forces aériennes royales néerlandaises
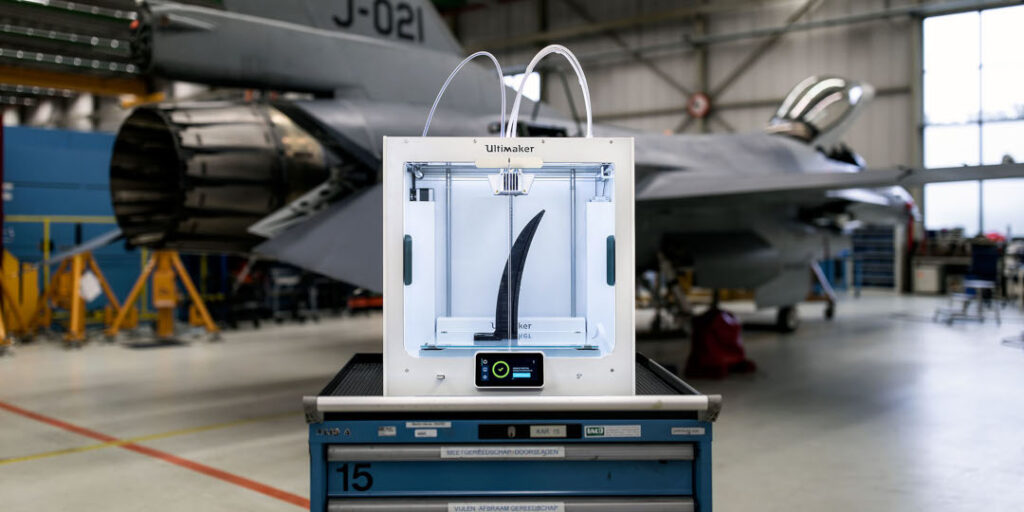
Accélérer la maintenance grâce à des outils imprimés en 3D Les forces aériennes royales néerlandaises sont les gardiennes du ciel des Pays-Bas. Leur flotte comprend un large éventail d’hélicoptères, d’avions de chasse et d’avions-cargos. Ces avions comportent de nombreuses pièces uniques, conçues sur mesure et difficiles à fabriquer avec des outils du commerce.C’est pourquoi les forces aériennes royales néerlandaises ont commencé à imprimer des outils sur mesure avec les imprimantes 3D d’Ultimaker. Ce cas client est disponible au format pdf. Remplissez le formulaire ci-joint pour recevoir le cas complet.
Ultimaker x Ford
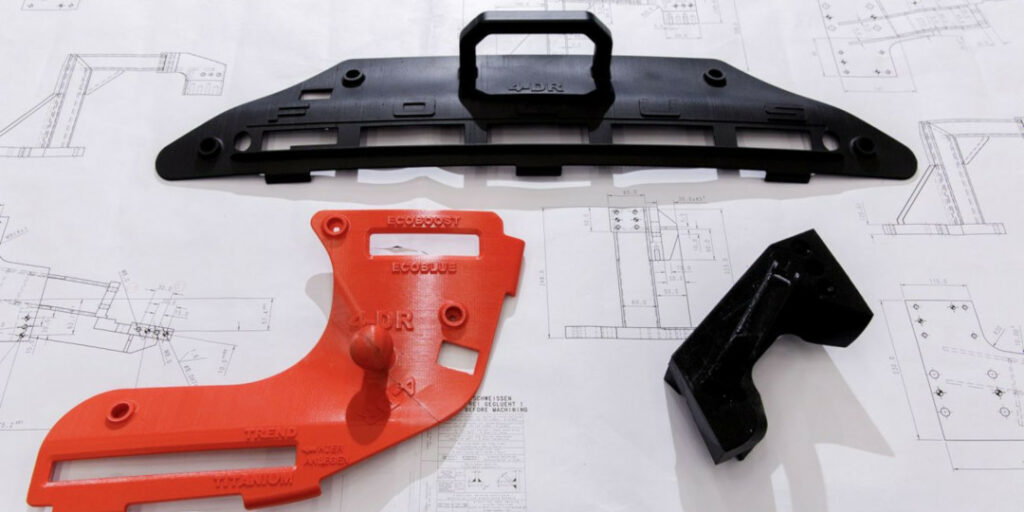
Réinventer la fabrication efficace avec l’impression 3D Depuis sa fondation en 1914, Ford a été un moteur de l’innovation dans le domaine de la fabrication automobile. Depuis la mise en place de la chaîne de montage mobile il y a 115 ans (également connue sous le nom de Fordisme) à l’utilisation actuelle de la fabrication additive, Ford réfléchit sans cesse à l’avenir pour accélérer la fabrication de ses véhicules grâce à une productivité, une ergonomie et un contrôle de la qualité accrus. Ce cas client est disponible au format pdf. Remplissez le formulaire ci-joint pour recevoir le cas complet.
Utilisation de la résine Grey Pro de Formlabs
Avis : Les bacs Resin Tank LT (Form 2) ou Form 3 Resin Tank V2 sont nécessaires pour imprimer avec de la Grey Pro Resin. La résine Grey Pro est une résine technique conçue pour les pièces haute précision, avec un allongement modéré et une faible déformation. Ces propriétés mécaniques font de la résine Grey Pro un matériau polyvalent utilisable pour une grande variété d’applications techniques, comme la modélisation de concepts et le prototypage fonctionnel. Très résistante à la déformation au cours du temps, la résine Grey Pro convient particulièrement à l’impression de pièces pour une manipulation ou un usage répétés. La résine Grey Pro s’imprime à 50 microns et 100 microns d’épaisseur de couche. Elle est recommandée pour les usages suivants : Elle n’est pas recommandée pour Remarque : Pour en savoir plus sur les performances ou les propriétés matérielles spécifiques de Grey Pro Resin, consultez la fiche de données de sécurité (FDS) et la fiche technique. Consultez toujours la FDS comme source principale d’information pour savoir comment manipuler les matériaux Formlabs correctement et en toute sécurité. Comparaison avec d’autres matériaux La résine Grey Pro est un matériau avec une formulation différente de celle de la résine Standard Grise. La Grey Pro est une résine technique offrant de meilleures performances comme un allongement plus élevé et une déformation moins importante. La résine Grise est une résine standard conçue pour la modélisation esthétique, de reproduction et de concepts. À vue d’œil, les pièces imprimées avec de la résine Grey Pro sont légèrement plus sombres et légèrement moins opaques que les pièces imprimées avec de la résine Grise standard. Les performances de la résine Grey Pro sont comparables à celles des autres résines techniques Formlabs. La résine Grey Pro permet d’imprimer des pièces précises et stables. D’autres matériaux, comme les résines Formlabs Tough 2000 Resin et Durable Resin, sont plus résistants aux chocs que la résine Grey Pro. Voir tableau ci-dessous pour comparer les performances des matériaux. Résine Grey Pro Formlabs Résine Tough 2000 Formlabs Résine standard Formlabs UTS (MPa) 61,0 46,0 65,0 Allongement (%) 13,0 48,0 6,2 Module (GPa) 2,2 1,9 2,2 HDT (°C, 1,8 MPa) 62,4 53,0 58,4 Pour en savoir plus sur les propriétés de chaque résine Formlabs, consultez les fiches techniques des matériaux. Impression avec la résine Grey Pro Les mêmes étapes essentielles que pour les autres résines Formlabs doivent être suivies pour l’impression avec de la Grey Pro Resin. Gardez à l’esprit ces quelques caractéristiques spécifiques pour la résine Grey Pro : Finition Lavez les pièces imprimées avec de la résine Grey Pro dans la Form Wash pendant 15 minutes. Après le nettoyage des pièces dans le bain d’alcool isopropylique, laissez-les sécher complètement avant la post-polymérisation. Conditions de post-polymérisation Pour connaître les conditions de post-polymérisation, référez-vous aux paramètres de température et de durée conseillés pour la Form Cure.
Utilisation de la résine Draft de Formlabs
Avis : Les bacs Resin Tank LT (Form 2) ou Form 3 Resin Tank V2 sont nécessaires pour imprimer avec Draft Resin V2. La résine Draft est le matériau Formlabs qui s’imprime le plus rapidement. L’impression de pièces en résine Draft est trois à quatre fois plus rapide qu’avec les autres résines classiques. Cette rapidité permet d’imprimer plusieurs versions d’un modèle le même jour ou d’imprimer des pièces volumineuses, remplissant complètement le volume d’impression, en moins de huit heures. Remarque : Pour en savoir plus sur les performances ou les propriétés matérielles spécifiques de Draft Resin, consultez la fiche de données de sécurité (FDS) et la fiche technique. Consultez toujours la FDS comme source principale d’information pour savoir comment manipuler les matériaux Formlabs correctement et en toute sécurité. Résine Épaisseur de couche Temps d’impression Résine Clear 25 microns50 microns100 microns 55 heures24 heures13 heures Résine Draft V1 300 microns 4 heures Résine Draft V2 100 microns200 microns 9 heures3 heures Ce matériau est recommandé pour : Ne convient pas pour : Comparaison avec d’autres matériaux Formlabs Résine Draft V1,post-polymérisation(à température ambiante) Résine Draft V1,post-polymérisation(60 °C) Résine Draft V2,post-polymérisation(à température ambiante) Résine Draft V2,post-polymérisation(60 °C) Résistance à la rupture par traction (MPa) 28 36 36 52 Allongement (%) 10 7 5 4 Module de traction (GPa) 1,3 1,6 1,7 2,3 Élasticité à la flexion (GPa) 0,9 1,5 1,8 2,3 Résistance au choc Izod (J/m) 35 21 29 26 Température de fléchissement sous charge à 1,8 MPa (°C) 44,3 50,1 53,0 74,0 Température de fléchissement sous charge à 0,45 MPa (°C) 50,7 63,4 44,0 57,0 Pour en savoir plus sur les propriétés des résines Formlabs, consultez les fiches techniques des matériaux. Impression avec la résine Draft La résine Draft s’imprime à 100 microns et 200 microns. La précision de la résine Draft dans les axes X et Y est comparable à celle des autres résines standard. La résine Draft n’est pas recommandée pour les pièces qui nécessitent des détails de surface fins. Recommandations relatives aux caractéristiques d’impression Vous réussirez vos impressions en résine Draft en suivant les instructions de conception de Formlabs. Les pièces en résine Draft sont imprimées avec des épaisseurs de couche plus grandes. Elles requièrent donc des conditions de conception légèrement différentes de celles applicables aux autres résines classiques. Parois avec supportsÉpaisseur minimale recommandée : 400 microns Parois sans supportsÉpaisseur minimale recommandée : 600 microns SurplombsRecommandée : 100 microns Faible inclinaisonAngle recommandé : 19° par rapport à l’horizontale Support horizontal, pont ou portéeÉpaisseur recommandée : 6000 microns Fil verticalDiamètre minimal recommandé : 300 à 1 500 microns Détail en reliefÉpaisseur minimale : 100 micronsÉpaisseur recommandée: 200 microns Engravure minimum d’un détailÉpaisseur recommandée : 400 microns Espacement minimalRecommandé : 500 microns Diamètre minimum d’un trouRecommandé : 500 microns Diamètre minimum d’un orifice de drainageRecommandé : 350 microns Finition Lavez les impressions en résine Draft dans de l’alcool isopropylique durant 10 minutes. L’alcool isopropylique pouvant être absorbé par le matériau, ne pas laisser tremper les pièces en résine Draft plus de 10 minutes. Nettoyez minutieusement les canaux internes et les parties en creux de la résine liquide, à l’aide d’une seringue ou d’air comprimé. Laissez les pièces sécher complètement après une éventuelle post-polymérisation. Poncez et peignez en suivant les mêmes opérations de finition que pour les résines classiques. Conditions de post-polymérisation La résine Draft ne nécessite pas de post-polymérisation. La post-polymérisation va augmenter la résistance à la rupture par traction et diminuer l’allongement. Pour connaitre les conditions de post-polymérisation, se référer aux paramètres de température et de durée conseillés pour la Form Cure.
Formlabs x Ashley Furniture
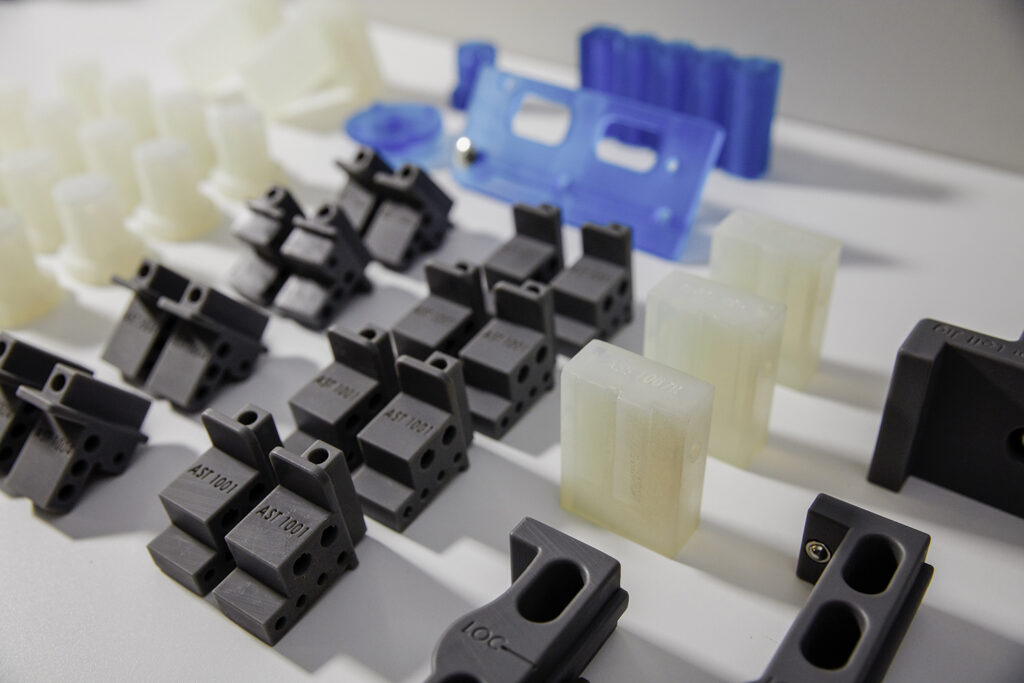
Ashley Furniture : d’une simple idée à 700 pièces imprimées en 3D dans l’usine Peu après qu’Ashley Furniture est installée sa première imprimante 3D stéréolithographique (SLA),l’un de ses ingénieurs de production a eu une idée. Était-il possible de remplacer des chevillesde positionnement usinées par des pièces imprimées en 3D ? Ces pièces finales permettraientd’éviter les longs délais de réalisation et les quantités minimales de commande imposées parla sous-traitance.La réponse était oui, mais elle a donné lieu à davantage de questions. Ce cas client est disponible au format pdf. Remplissez le formulaire ci-joint pour recevoir le cas complet.
Formlabs x Braskem
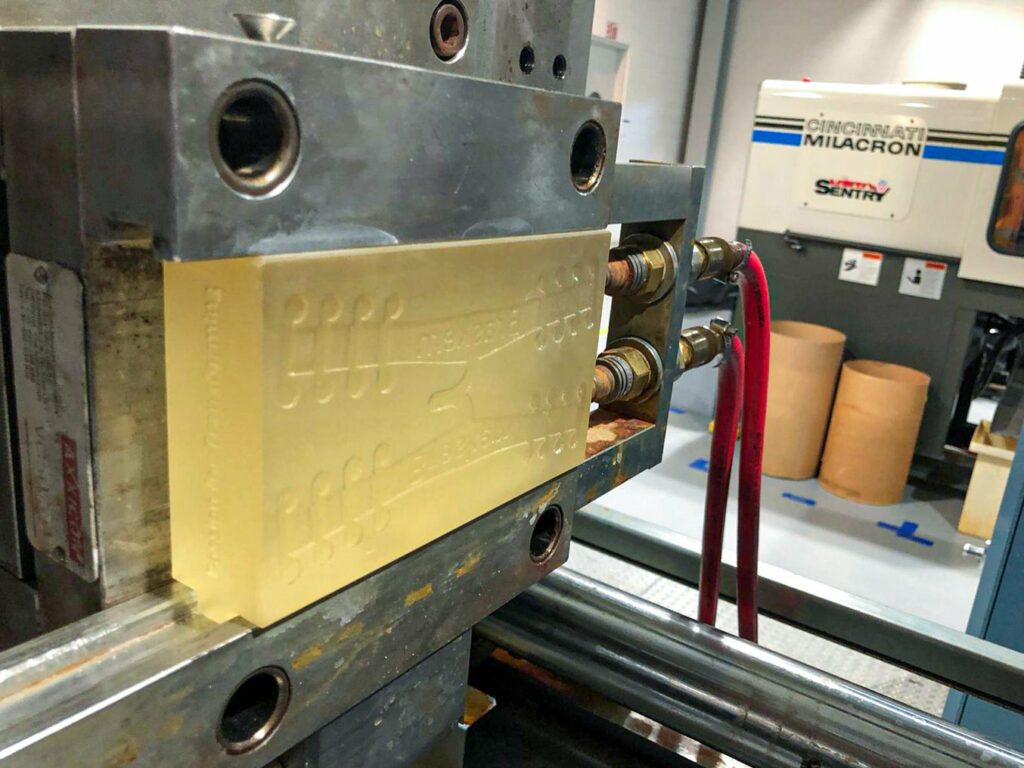
Comment Braskem a utilisé l’impression 3D pour le moulage par injection La fabrication de moules est utilisée dans tous les secteurs par des concepteurs de produits,des entrepreneurs et des enseignants pour réaliser des productions rapides, prototyper desmoules complexes, tester la production avec des plastiques d’usage final, et bien d’autresapplications. Le moulage par injection en particulier est un procédé polyvalent qui sert enproduction de grands volumes.Pour les entreprises qui utilisent le moulage par injection, associer une imprimante 3D Formlabsà la fabrication de moules permet aux ingénieurs et aux concepteurs d’obtenir rapidementdes moules à un coût abordable. En plus de compléter le procédé de fabrication, les moulesd’injection imprimés en 3D s’obtiennent plus rapidement et sont moins coûteux que ceuxréalisés par usinage CNC ou par d’autres procédés traditionnels.Formlabs s’est entretenu avec Michelle Sing et Jake Fallon, ingénieurs de développementtechnologique, Collin Azinge, ingénieur en procédés de fabrication additive, et Fabio Lamon,responsable mondial des technologies de fabrication additive de Braskem, l’un des leadersmondiaux de la pétrochimie, pour qu’ils racontent leur première expérience du moulage parinjection avec une pièce imprimée en 3D. Ce cas client est disponible au format pdf. Remplissez le formulaire ci-joint pour recevoir le cas complet.
Ultimaker x Schubert
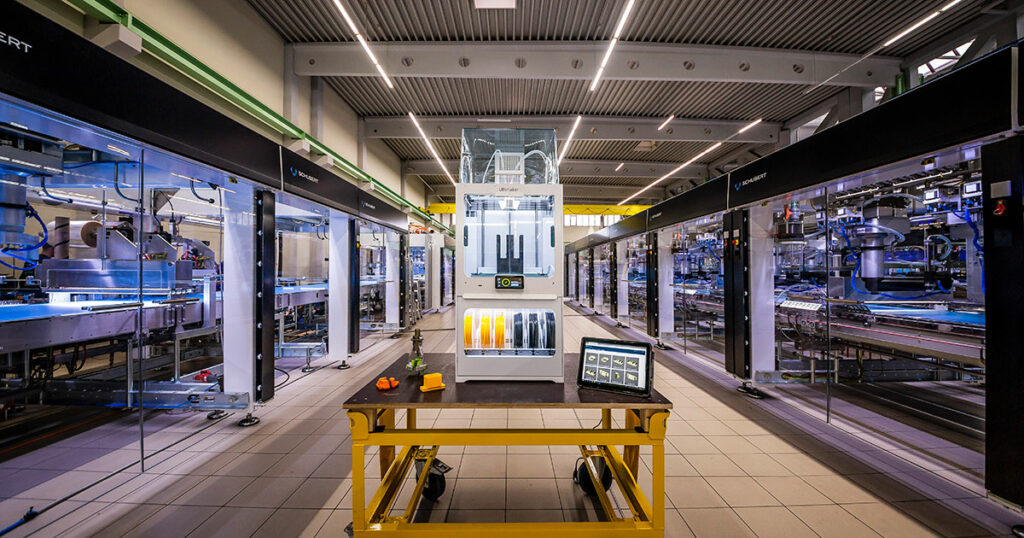
Un entrepôt numérique pour une fabrication sur-mesure Schubert utilise l’impression 3D pour fournir les outils nécessaires à ses machines d’emballage haute performance et à l’épreuve du temps afin de les rendre davantage polyvalentes et faciles à utiliser. Ce cas client est disponible au format pdf. Remplissez le formulaire ci-joint pour recevoir le cas complet.
Ultimaker x Killa Design
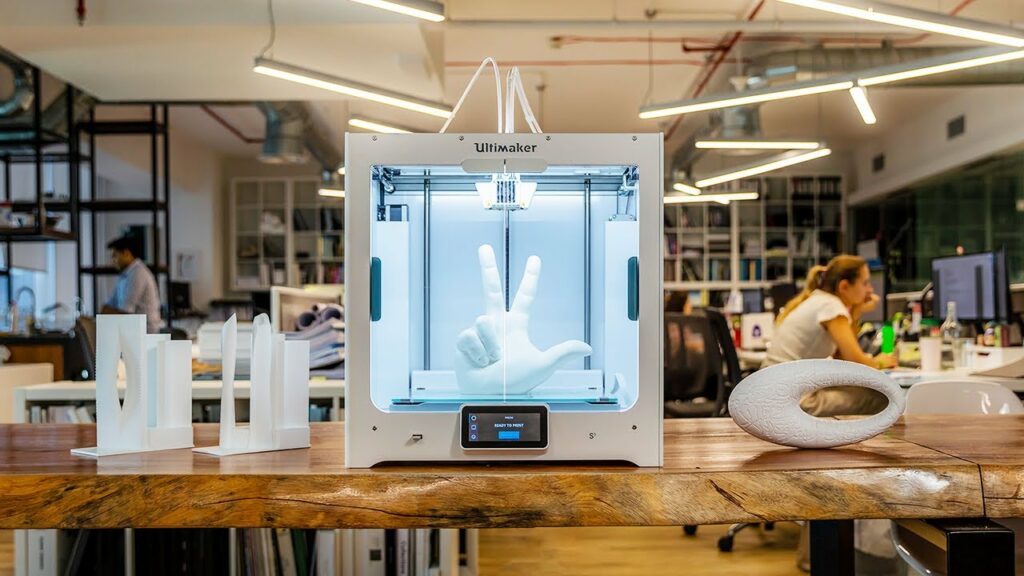
Imprimer en 3D les bâtiments de demain Au cours des deux dernières décennies, les architectes ont bénéficié d’une plus grande liberté de conception grâce à des outils de CAO et des techniques de construction de pointe. Les conceptions deviennent plus organiques, agiles et dynamiques, tout en permettant aux entreprises d’architecture de repousser les limites du possible. Killa Design est l’une de ces entreprises.Basée à Dubaï, Killa Design se spécialise dans les designs uniques, iconiques et intemporels, cela inclut le premier espace de bureau imprimé en 3D occupé au monde ainsi que l’une des structures les plus complexes jamais construites. Ce cas client est disponible au format pdf. Remplissez le formulaire ci-joint pour recevoir le cas complet.